Quartz stone is a kind of abbreviation of the plate produced by the current quartz stone plate manufacturer because the quartz content of the main component of the plate is as high as more than 93%, so it is called quartz stone.
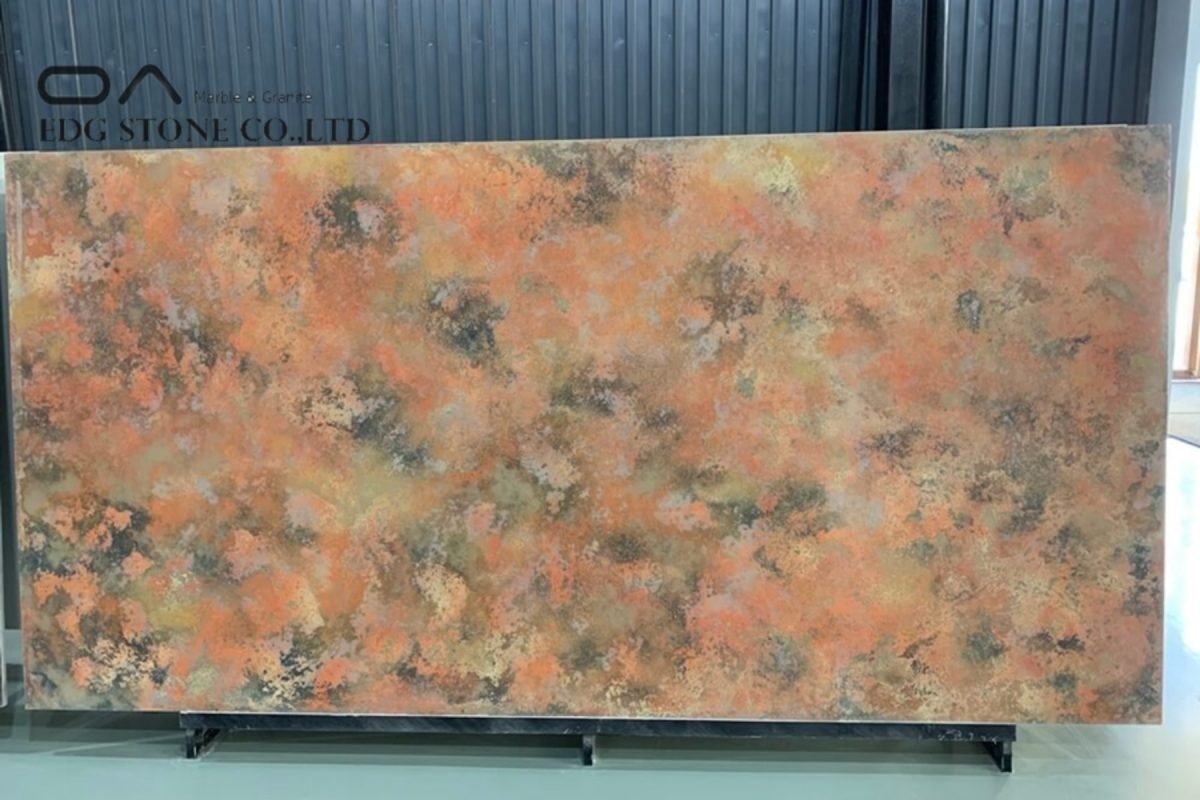
Calacatta quartz countertop
Quartz stone process description:
1. Raw material collection: procurement of raw and auxiliary materials such as glass, quartz, resin, etc.
(1) Resin
(2) Quartz sand
2. Material selection: use fans, iron removal equipment, and manual selection to remove impurities and iron filings in granular raw materials.
3. Batching: After the material selection is completed, the material is transported into the mixing system. The material is fully mixed in the gravity-free mixer, eliminating the problem of material color difference and uneven particles. After the mixing is completed, it is conveyed to the corresponding batching bin, and the batching system automatically batches the material during production.
4. Stirring: Fully stir and mix unsaturated polyester resin, pigments, additives, and granular powder.
5. Cloth: The stirred mixed material enters the cloth car through the conveyor belt, and then the material is evenly distributed into the cloth mold frame by the cloth car.
6. Vacuum high-frequency vibrating platen: After the distribution is completed, it is transmitted to the press equipment and vibrated and pressed under the vacuum condition of -0.1MPa.
7. Heating and curing shaping: After pressing, the blank is heated and formed at 85-110 °C in the curing oven.
8. Calibration grinding: After the blank is cured, it is cooled and cooled for 24 hours, and then enters the calibration equipment for calibration.
9. Polishing: After the thickness is fixed, the water grinding and polishing are carried out through the 20-head polishing machine. According to different needs, polish to a gloss of 40-70°.
10. Inspection: inspect the appearance quality of the plate.
11. Cutting board: use vertical and horizontal cutting and bridge cutting machine equipment to cut the product to the required size.
12. Packaging and warehousing: After the cut products are air-dried, they are packaged and stored in the warehouse.
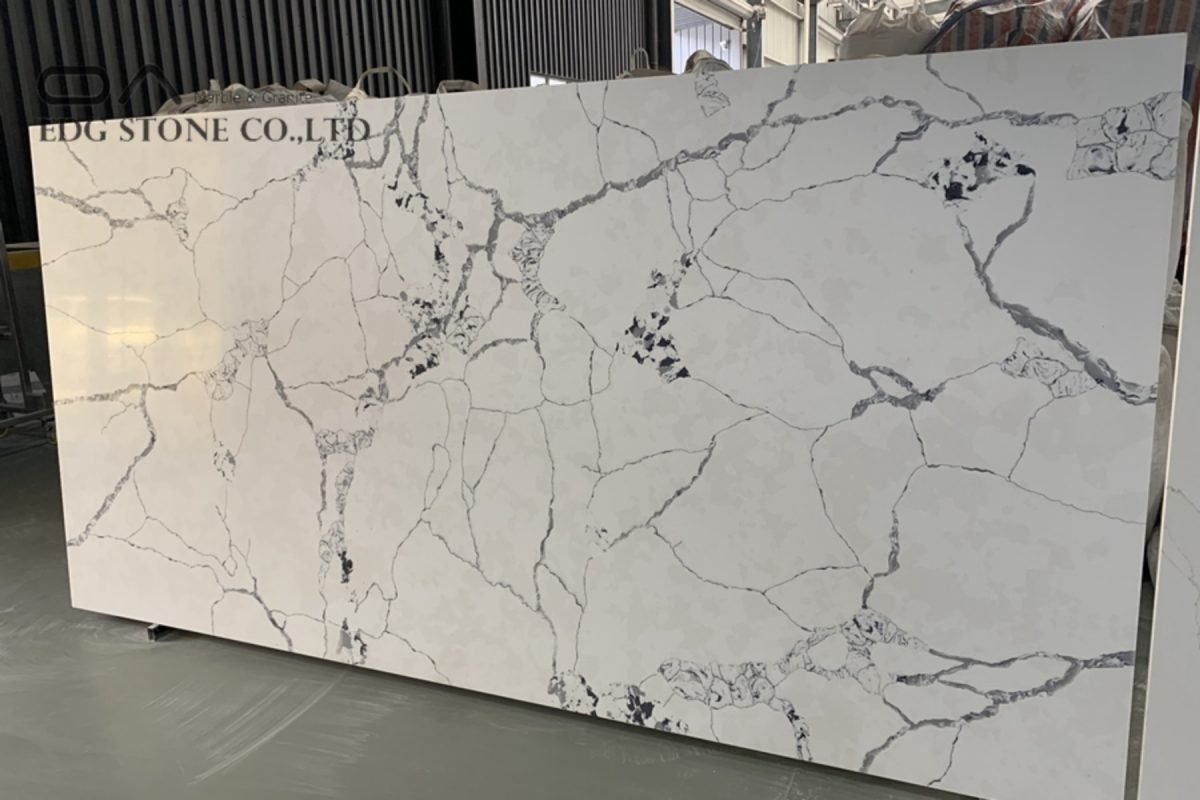
Calacatta quartz countertops
Quartz stone finished product processing technology:
Quartz stone processing is an important part of ensuring the quality of countertops. No matter how good the quartz stone slab is, there will be quality problems if it does not follow the strict quartz stone processing method.
The processing requirements of quartz stone are, in principle, the same as the processing of natural stone, which is made up of natural granite and granite. The operator who processes quartz stone should have experience in processing natural stone, and the operator who has no experience in processing ordinary man-made stone must be trained before he can take up his post in principle.
Necessary processing tools: multi-functional marble cutting machine (cutting and cutting, grinding edge chamfering), grinding machine (with special diamond grinding disc, resin grinding disc), cantilever water grinding and polishing machine, gong machine (with quartz special gong head), curve data, A-clip, G-clip, small blade, triangular glass fixture, wiring socket, etc.
Special glue: marble glue (white, transparent), quartz stone special glue (factory preparation), quartz stone special dry glue (factory preparation), curing agent.
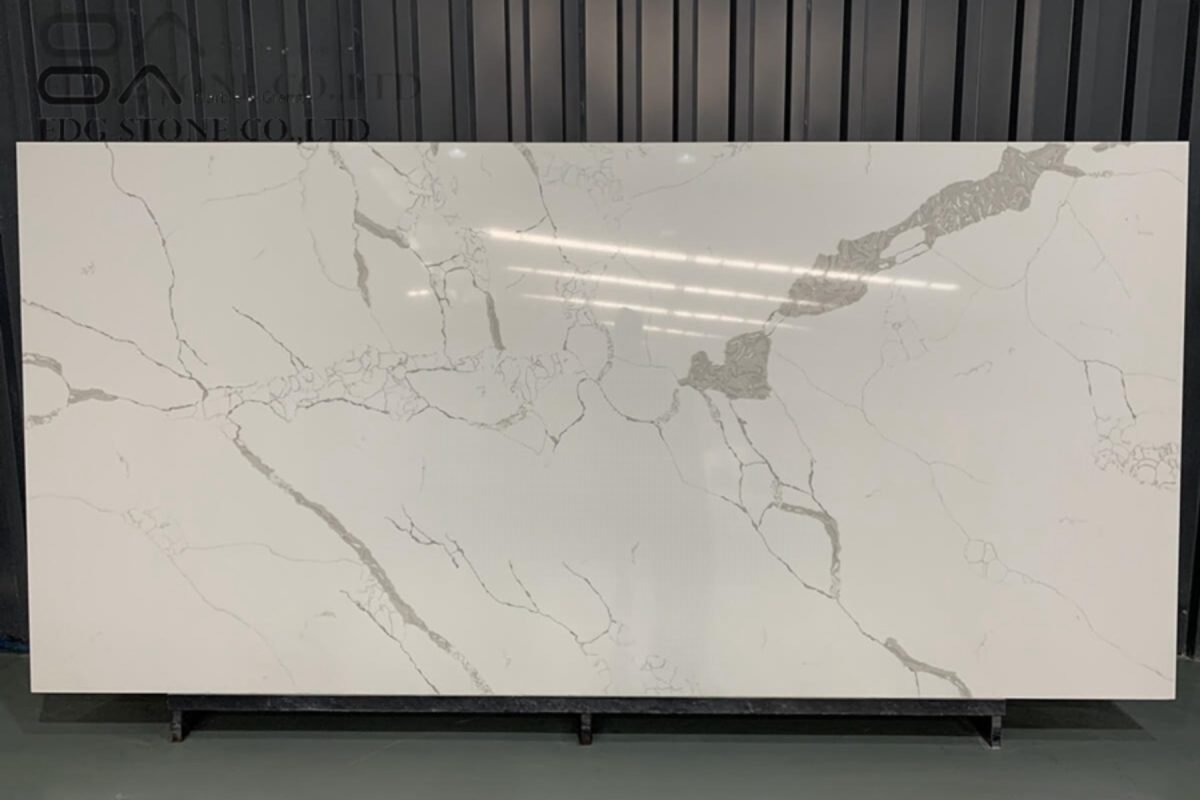
Calacatta quartz counters
Processing precautions:
Because the hardness of quartz stone is too high, its plasticity is not as strong as artificial stone, and the processing technology is higher than that of artificial stone.
(1) Connection: Quartz stone connection is generally spliced at 45 degrees. When the flat connection is carried out, the connecting surface must be straightened with a straight knife gong, and the docking can be carried out seamlessly.
The remaining glue at the joint should be removed with a small blade after the gel but not hard, and then polished when the glue is completely hardened, and the grinding range should not be expanded.
After the quartz stone is connected, there will generally be traces like a line, but it is not easy to see without looking carefully, and it does not affect the appearance.
(2) Opening: When opening the furnace hole, there should be a backing plate at the bottom of the quartz stone plate, which cannot be completely suspended, and the bearing force should be uniform to prevent cracking in the opening process due to uneven force.
Before opening the hole, the bottom four sides and the middle of the quartz stone are reinforced, and then punched at the four corners of the furnace hole (the drill bit must be a diamond drill bit of high hardness, and the stone processing tools and supplies of Yunfu are sold in the store), and then use the wire cutting machine to cut the square slowly and evenly when cutting, the plate can not be cut through at one time, it should be cut in two steps, the first step is to cut 1/3 of the thickness of the plate, and the second step is to cut through the plate to prevent the plate from cracking.
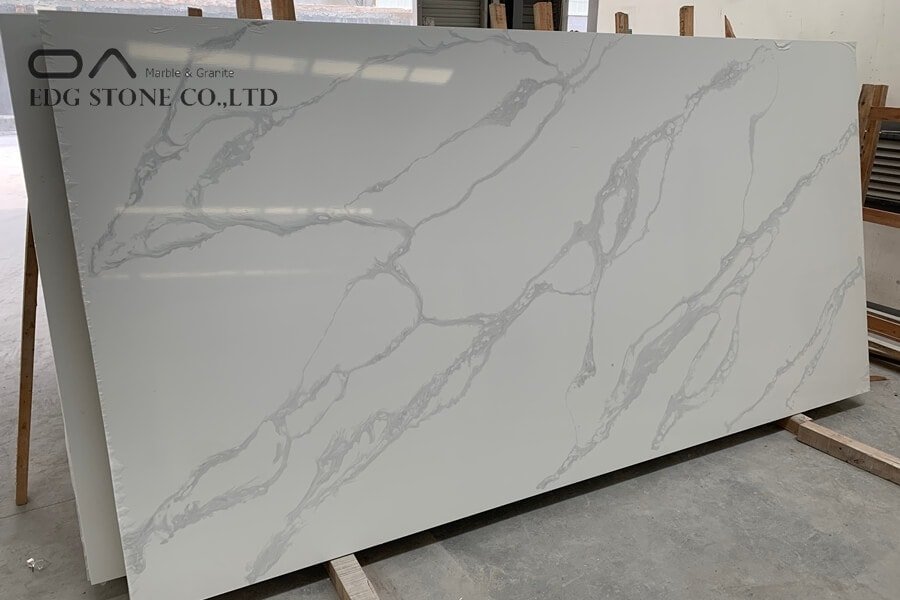
Quartz Surfaces Manufacturer
After the furnace hole is cut into a square, the four corners of the furnace hole are ground into an arc angle with an angle grinder, the arc radius is not less than R10mm, and the back of the four corners of the furnace hole is thickened with a small plate of about 120×120mm, and then the angle grinder grinds it into a corresponding arc, and the four sides are thickened with quartz stone plates with a width of more than 30mm. In addition, the distance between the furnace hole edge and the back waterproof edge is not less than 70mm.
(3) Edging and chamfering: use hard diamond water grinding discs, first 50#, then 150#, and then 300#; when polishing, start with 500# water grinding discs, and then use 800#, 1000#, 1500#, 2000# water grinding discs for polishing.
Note that the diamond water grinding disc must be made of hard material, which must be emphasized with the supplier. The size of the water grinding disc is 3 inches or 4 inches, which can be used according to the needs of use.
(4) Glue use: The glue must be fully stirred before the glue is used. The glue curing agent is the same as the ordinary artificial stone curing agent, and the relationship between the amount added and the temperature is as follows:
When the temperature is below 10 °C, the amount of curing agent added is 1.5-2% of the glue;
When the temperature is 10°C–20°C, the amount of curing agent added is 1% of the glue;
When the temperature is 20°C–30°C, the amount of curing agent added is 0.5-0.8% of the glue;
When the temperature is above 30°C, the amount of curing agent added is 0.5% of the glue.